Topics
Ontego can do more than just mobile data entry, as shown by the project at Abbott's Zurich location. Here, the workflows in the warehouse and production have been largely automated—with Ontego serving as the central data hub between SAP, the storage lift, and the label management system.
Abbott is a global provider of medical technology and branded generic drugs. In Switzerland, the company produces cardiovascular technologies such as left ventricular assist devices (LVADs). An Ontego solution has been in use in their material management department there since 2020. In contrast to classic mobile data entry with SAP, Ontego at Abbott functions as the central data hub in the midst of various peripheral systems.
Time-Consuming Manual SAP Postings
The Abbott site in Zurich has spatial restrictions that require an efficient use of space. The focus is on production, with materials management and warehousing as supporting processes. Within the Abbott group, SAP is the leading system, which was also introduced at the Technopark as part of the site integration. "We always shied away a bit from making a lot of SAP postings," recalls Thomas Locher, Senior Manufacturing Engineer. "Sitting at a PC, calling up the transactions in the SAP GUI, and entering the data by hand—all of that was a very laborious procedure."
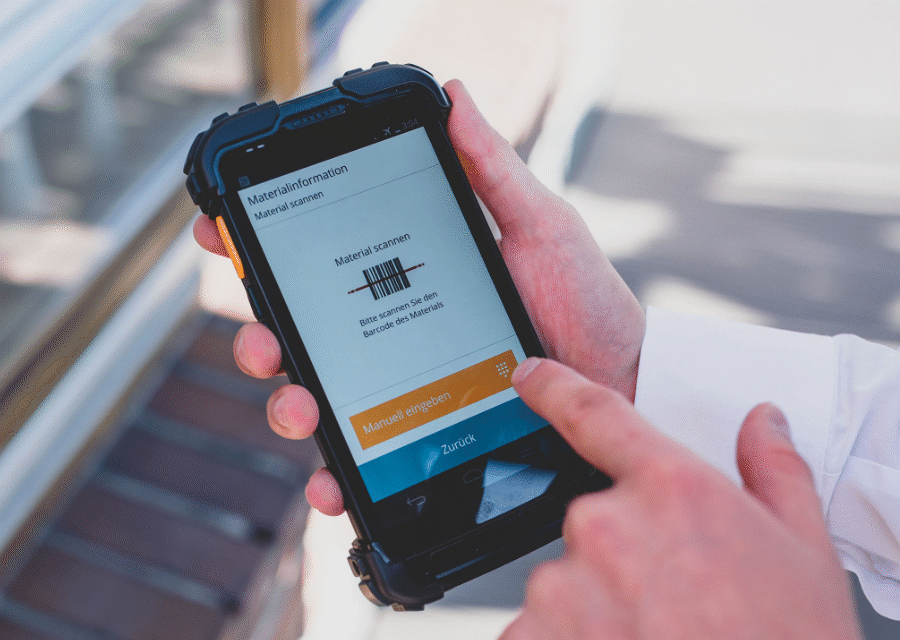
Learn everything about modern mobile SAP apps in warehouse and production.
Strict Regulation of the SAP System
The integration into the corporate structure presented a key challenge. As the leading system in the company, SAP is centrally managed and heavily protected by Corporate IT. Access to SAP functions is only possible via a few select interfaces. Locher's assessment in retrospect: "SAP was introduced here so that we would have tracking for everything, but not to make life easier." As a consequence, Locher and his colleagues began looking for a solution that would provide exactly the simple and automated processes they needed.
Goal: Automation in the Material Flow
Thus, the decision was made to largely digitize the data entry processes in production and the warehouse. "Our main desire was actually complete automation," confirms Locher, and he lists several aspects that were to be achieved with a comprehensive project:
- Completely digital recording of lot numbers
- Consistent use of barcode labels on materials and finished products
- Integration of SAP with warehouse hardware and software
.jpg)
Components in the Automated Material Flow
Abbott Switzerland uses various components for the digital processing of its material flow:
- SAP as the leading backend system
- Storage lift systems
- Label management software
- Label printers
- Software for mobile data entry
The challenge was to connect these individual systems. While some systems have interfaces to SAP, the ERP system itself is not equipped to control the data flow between all the individual components. "So we decided on a piece of software to sit in the middle, one that connects all these interfaces and also caters to our needs within the process flow," explains Locher, "namely, a software that supports the user at the right moment and forwards the data to the right place."
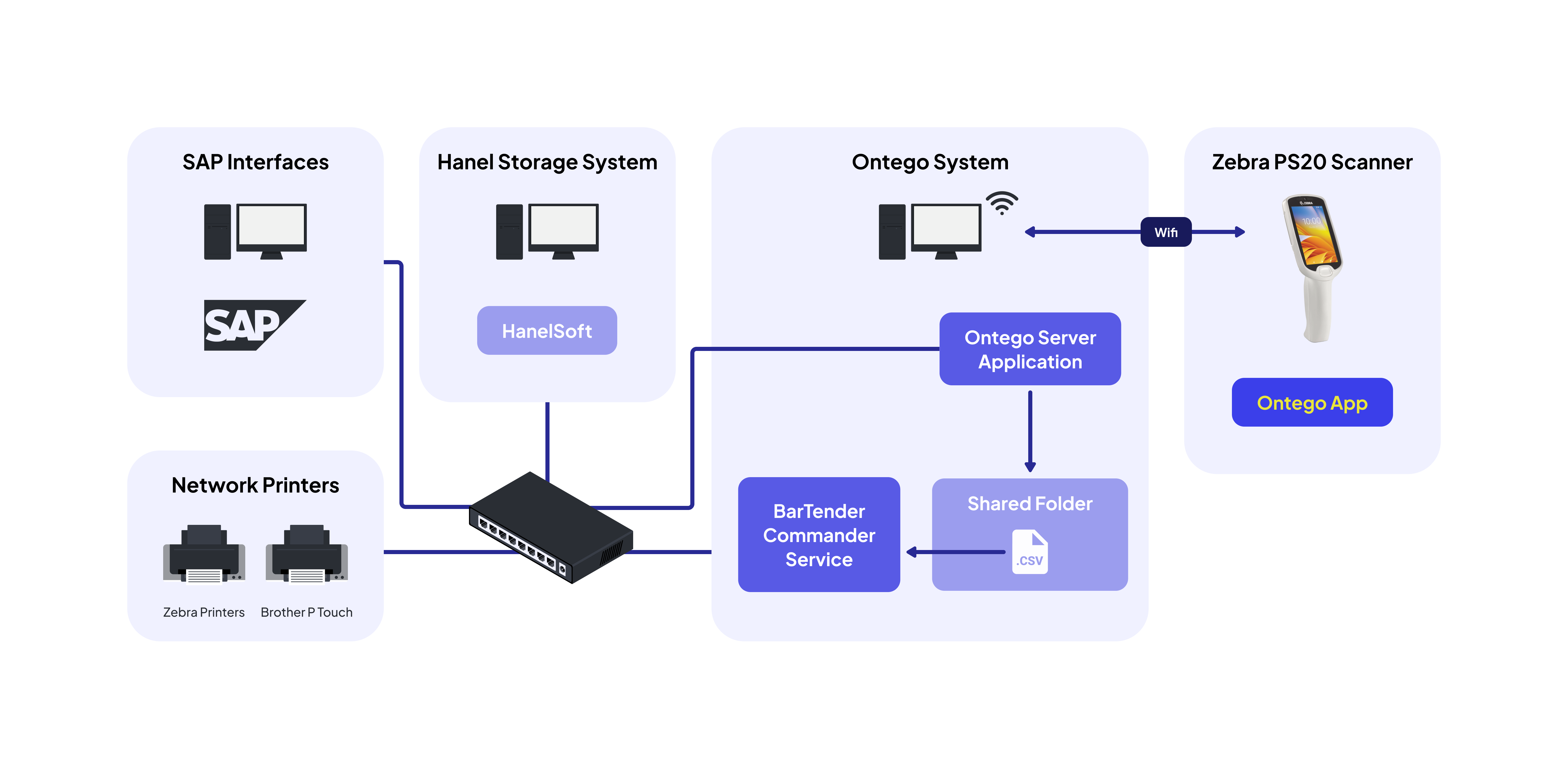
Source : commsult Digital Assets
Ontego as the Central Interface
In this case, the data hub desired by Abbott is mapped via the Ontego platform. In addition to its classic application—mobile data entry on handhelds—supplementary server-based functions are used in Zurich. Central to this is the Ontego Mobility Layer, a special server component. Locher puts it nonchalantly when he says that Ontego does nothing more than read data from barcodes via the mobile app and forward it in the background to SAP and other systems. This amounts to a total of between 1,000 and 2,500 transactions every month.
Software that supports the user at just the right moment and sends the data to the right place
— Thomas Locher, Senior Production Engineer, Abbott Zurich
Digital Order Handover to the Storage Lift
One of the first decisions was to acquire automated small parts warehouses, or rather, storage lift systems. Three systems from the Swiss specialist Hänel were installed. And the effect was enormous: "Previously, half of our production hall was filled with racks. We've now gained at least 50 square meters thanks to the vertical storage lifts," summarizes Locher. The problem was that the Hänel lifts have their own inventory management system, which was not synchronized with the inventory management in SAP. This led to manual reconciliation processes and a corresponding expenditure of time.
Today, Ontego handles the synchronization:
- An initial work order for putaway or retrieval from the lift is displayed on the mobile device.
- Ontego sends material numbers, etc., to the lift.
- The employee puts away or retrieves the items and simply confirms the transaction at the lift.
- Ontego communicates with the lift and receives information about the posting.
- Ontego automatically synchronizes the inventory change at the lift with SAP.
The time savings of this digital workflow become tangible through the elimination of manual order entry at the storage lift, which previously required the input of the following data:
- Material number (7 digits)
- Batch number (9 digits)
- Date for FIFO strategy (8 digits)
In total, the entry of this data by an employee at the lift screen took between 30 and 60 seconds per job. On average, between 250 and 400 warehouse movements related to the Hänel lifts are recorded each month. This means that every month, Abbott saves between 2 and 4 hours of work time solely through the automation at the storage lift.
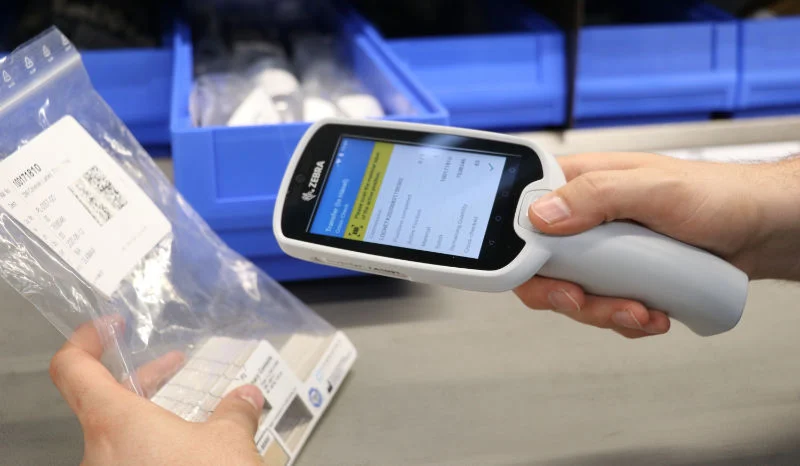
Integration with Label Management
At Abbott in Zurich, over 100 different labels are used in production and the warehouse. Employees print approximately 5,000 labels monthly. Where manual entries were previously required, today a scan and a printer selection are all that's needed to start the print job. A specialized software solution manages the label templates, and Ontego communicates with this label solution as well.
In practice, it looks like this: If an operator wants to print a product label, they start on the handheld by scanning a work order. Ontego receives the order details, such as material, expiration dates, batches, etc., from SAP. Ontego can then assign the material number to the correct label and provide the necessary data. Ontego passes this consolidated data to the label software, where the label fields are populated and print jobs are prepared. The employee can still select the appropriate printer on the mobile device. And that's it. At the printer of their choice, the employee then receives one or more labels, depending on the order, which they can then affix to the materials as specified in the work order.
The process described above at a glance:
- Scan of a Work Order
- Selection of a printer on the handheld
- The printing begins
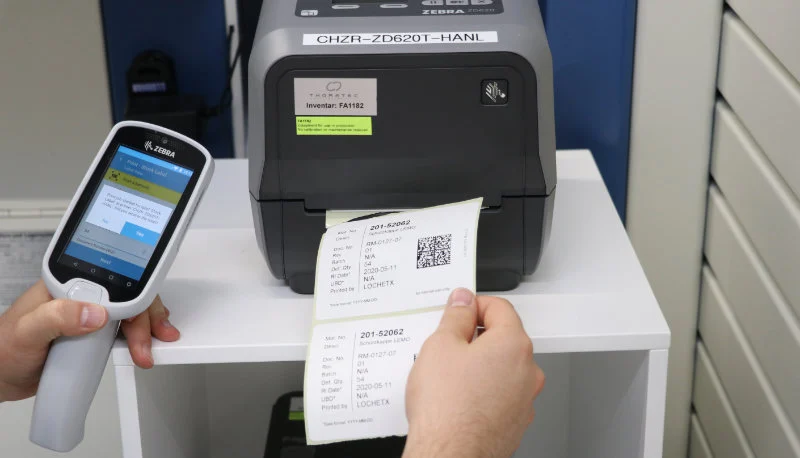
Validation of the Mobile Solution
As a medical technology company, Abbott is subject to strict regulations in a wide variety of areas—similar to the pharmaceutical sector, where software is tested according to the specifications of the "Good Automated Manufacturing Practice Supplier Guide for Validation of Automated Systems in Pharmaceutical Manufacture” (GAMP).
The software used in the project described here also went through a thorough validation process, which was overseen by Locher. The engineer emphasizes that the validation went beyond a mere check of functionalities. They tested whether all requirements were met in the areas of data security, data integrity, cybersecurity, etc. From his experience, the extensive process is worth the effort, and he recommends not just running through simple test cases, but also defining variations and rare scenarios.
Conclusion
Demanding production and logistics processes within a very confined space—these are the general conditions that the employees at Abbott's Technopark in Zurich must handle. The solution is a highly automated material flow, from goods receipt through production to shipping. In this setup, Ontego is not only used for mobile data entry but also supplements central functions in the data exchange between the participating systems via the Ontego middleware component.
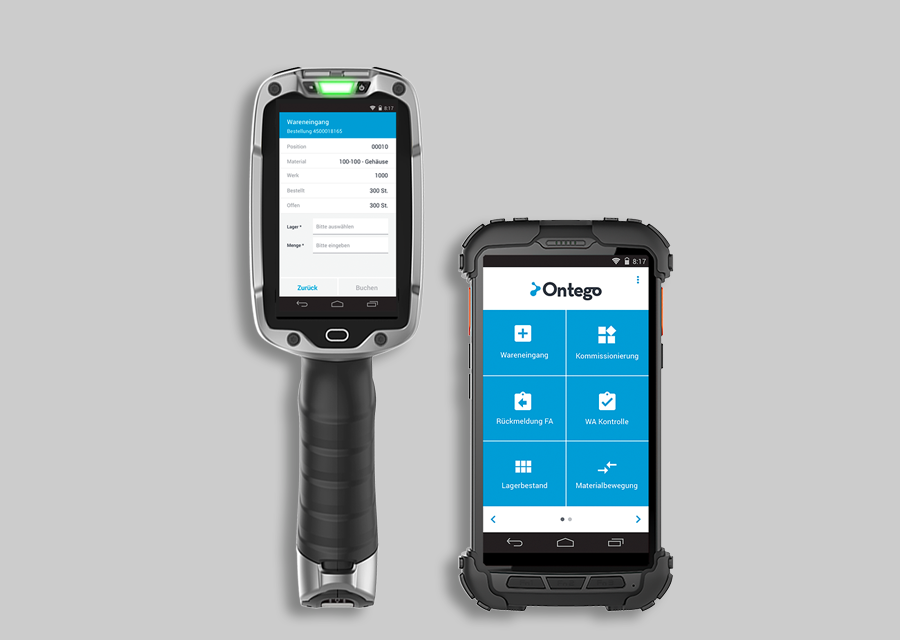
Optimize your warehouse effortlessly and cost-effectively with the Ontego subscription model.